
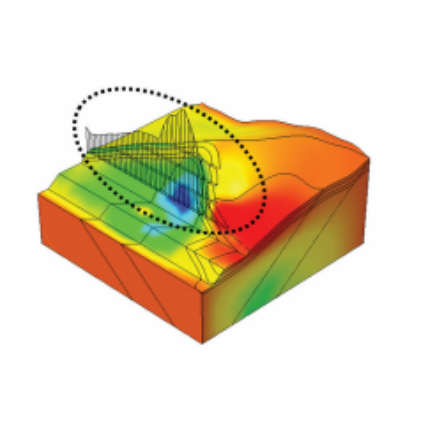


The 21st century has been called the century of human exploitation of underground space.
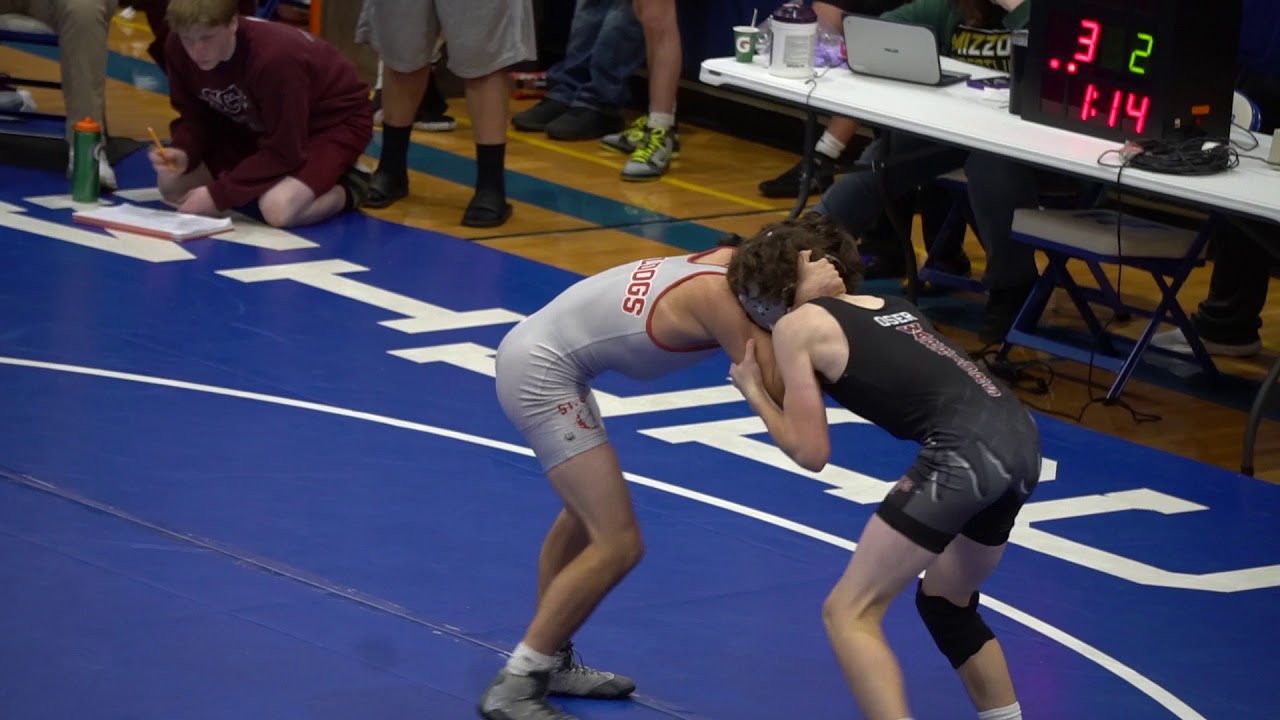
Therefore, the use of any statistical parameters could be misleading if not considered in an appropriate way. It was found that although some parameters increase in value as the deterioration level increases, they show almost no change or even decrease when the number of cracks increases. Multiple cracks were also introduced at different locations and the vibration response along with the statistical parameters were obtained again for a general case of degradation (increase in crack depth, crack number and crack locations). They showed different degrees of sensitivity toward the crack depth. In addition, various statistical time domain parameters were considered. The change in the mesh stiffness and the vibration response were found to be consistent with previously published works. The effect of one crack with different levels was studied thoroughly. The vibration simulation results of the gearbox were by obtained using Simulink/Matlab. The model developed for calculating the stiffness with the crack permitted to update the physical parameters of the second-degree-of-freedom equations of motions describing the vibration of the gearbox. A simplified six degrees of freedom nonlinear lumped parameter model of a one-stage spur gear system is proposed to study the vibration with and without cracks. As cracks alter significantly the stiffness of the tooth, finite element software is used to determine the stiffness variation with respect to the angular position, for different combinations of crack orientation and depth. In contrast to other published papers, this work incorporates the possibility of multiple simultaneous cracks with different depths. The objective of this study is to develop a numerical model that simulates the effect of teeth cracks on the resulting gears vibrations and permits consequently to perform an early fault detection. One of the common gear failure causes is tooth fatigue crack however, its early detection is still a challenging task. Gears are important components with a vital role in many rotating machines.
